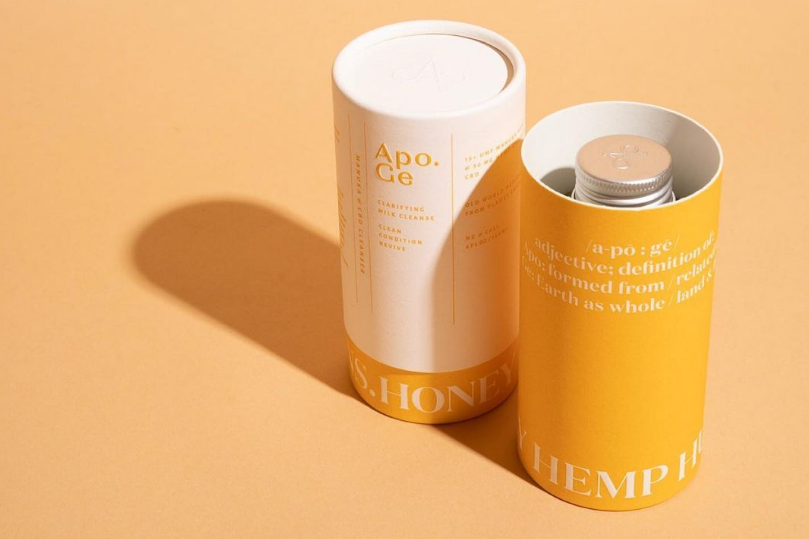
Eco-Friendly Cosmetic Paper Tube Packaging: A Green Revolution in Beauty
In today’s environmentally conscious world, the beauty industry is undergoing a significant transformation.
This article delves into the fascinating process of how kraft paper packaging, particularly paper tubes, are made. Whether you’re a business owner looking to make environmentally friendly choices or simply curious about the journey from raw material to finished product, this comprehensive guide will provide valuable insights into the world of kraft paper tube manufacturing.
Understanding how kraft paper packaging is made is crucial for several reasons. First, it helps businesses make informed decisions about their packaging choices, aligning with sustainability goals. Second, it allows consumers to appreciate the eco-friendly nature of these products. Lastly, it sheds light on the innovative techniques used by leading paper tube manufacturers to create durable, versatile, and environmentally friendly packaging solutions.As we explore the manufacturing process, you’ll gain insights into the sustainability, versatility, and quality of kraft paper tubes. This knowledge can help you make better packaging decisions for your business or personal use.
Kraft paper, the foundation of kraft paper packaging, is a sturdy, brown paper known for its strength and durability. The production process begins with wood chips, typically from pine trees, which are cooked in a solution of sodium hydroxide and sodium sulfide. This process, known as the kraft process, separates the cellulose fibers from lignin and other wood components.The resulting pulp is then washed, bleached (if white kraft paper is desired), and pressed into sheets. The kraft process yields paper that is significantly stronger than paper made through other methods, making it ideal for packaging applications.
Paper tube manufacturers use a process called spiral winding to create kraft paper tubes. Here’s a step-by-step breakdown of the process:
This process allows for the creation of tubes in various diameters and lengths, catering to different packaging needs.
The spiral winding process is versatile, allowing paper tube manufacturers to create a wide range of products. Some common types include:
Quality control is a crucial aspect of kraft paper tube manufacturing. Leading paper tube manufacturers employ several strategies to ensure their products meet high standards:
These measures help ensure that the final products are sturdy, uniform, and fit for their intended purpose.
Sustainability is at the heart of kraft paper tube manufacturing. Here’s how the process aligns with eco-friendly principles:
By choosing kraft paper tubes, businesses can significantly reduce their packaging’s environmental impact.
Customization is a key strength of kraft paper tube packaging. Manufacturers offer various options:
This flexibility allows businesses to create packaging that perfectly suits their products and brand identity.
While kraft paper tube manufacturing is a well-established process, it’s not without challenges:
Overcoming these challenges requires expertise, advanced technology, and continuous process improvement.
Technological advancements have significantly enhanced the kraft paper tube manufacturing process:
These innovations have made the production process more efficient, consistent, and capable of meeting diverse packaging needs.
The future of kraft paper tube manufacturing looks promising, with several trends on the horizon:
These developments will likely make kraft paper tubes an even more attractive packaging option in the coming years.In conclusion, the process of manufacturing kraft paper tubes is a blend of traditional papermaking techniques and modern technology. As businesses and consumers increasingly prioritize sustainable packaging solutions, understanding this process becomes more valuable. Kraft paper tubes offer a versatile, customizable, and environmentally friendly alternative to many conventional packaging materials.Key takeaways:
By choosing kraft paper tubes, businesses can embrace a packaging solution that’s not only effective and customizable but also aligns with environmental sustainability goals.
In today’s environmentally conscious world, the beauty industry is undergoing a significant transformation.
Are you a coffee roaster looking to make your brand stand out on the shelves?
In the competitive world of fragrance marketing, packaging plays a crucial role in capturing consumer attention and conveying brand prestige.
In recent years, paper tube packaging for salt and spices has gained significant popularity among consumers.
Are you wondering if those trendy paper tube packages can really keep your salt fresh for the long haul?
In today’s environmentally conscious world, the packaging industry faces a unique challenge: creating products that are both safe for children and eco-friendly.
In today’s eco-conscious world, businesses are increasingly turning to sustainable packaging solutions.
Paper tube packaging has emerged as a game-changer in the world of sustainable packaging solutions.
In today’s packaging landscape, product safety is paramount.
© All Rights Reserved 2024