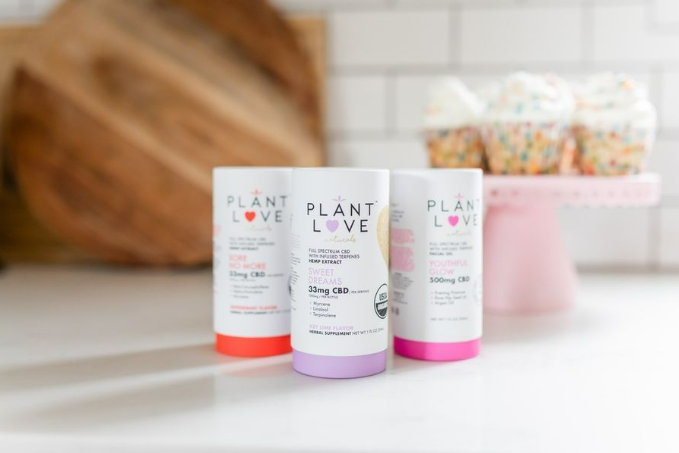
Customizing Food Supplement Paper Tubes: A Brand’s Ultimate Packaging Solution
Are you looking to elevate your food supplement brand with unique, eye-catching packaging?
This article delves into the fascinating world of paper tube production, exploring everything from custom-made solutions to ready-to-use options. Whether you’re a business owner looking to optimize your packaging or simply curious about the process, this comprehensive guide will provide valuable insights into the art and science of paper tube manufacturing.
Paper tubes, also known as cardboard tubes or cores, have become increasingly popular in the packaging industry due to their versatility, eco-friendliness, and cost-effectiveness. These cylindrical containers are used for a wide range of applications, from shipping posters and artwork to packaging food products and cosmetics.The popularity of paper tubes stems from several factors:
Cost-effectiveness: Compared to other packaging materials, paper tubes offer a balance of quality and affordability.
The production of custom paper tubes involves several steps, each crucial to ensuring the final product meets the customer’s specifications. Here’s an overview of the manufacturing process:
“Custom paper tubes are like fingerprints – no two are exactly alike. Each one is tailored to meet the unique needs of the product it will house.” – Industry expert
Producing high-quality paper tubes requires attention to several critical factors:
Consistency is key in custom paper tube manufacturing. Here are some strategies employed by manufacturers:
In today’s environmentally conscious market, the eco-friendly nature of paper tube packaging is a significant advantage. Here’s why:
Custom paper tube packaging offers numerous benefits for businesses across various industries:
While paper tube manufacturing has many advantages, it also faces certain challenges:
When compared to other packaging solutions, paper tubes offer several distinct advantages:
Aspect | Paper Tubes | Plastic Containers | Cardboard Boxes |
Customizability | High | Medium | High |
Eco-friendliness | High | Low | High |
Durability | Medium | High | Low-Medium |
Cost | Medium | Medium-High | Low |
Weight | Light | Medium | Light |
Recyclability | High | Low-Medium | High |
The paper tube packaging industry is continually evolving. Some recent innovations include:
Selecting the right paper tube manufacturer is crucial for ensuring your packaging meets your specific requirements. Consider the following factors:
“Choosing the right paper tube manufacturer is like finding a perfect dance partner – you need someone who can match your rhythm and help you shine.” – Packaging industry consultant
In conclusion, paper tube packaging offers a versatile, eco-friendly, and customizable solution for a wide range of products. By understanding the production process, key considerations, and latest innovations, businesses can leverage this packaging option to enhance their product presentation, protection, and sustainability efforts.
Are you looking to elevate your food supplement brand with unique, eye-catching packaging?
In the world of luxury fragrances, packaging plays a crucial role in protecting and presenting the product.
In today’s eco-conscious world, the demand for sustainable packaging solutions has never been higher.
Paper tubes are transforming the packaging industry, offering a sustainable and versatile alternative to traditional materials.
Sustainable Packaging Revolution: How Paper Tubes Are Reducing Waste
In today’s eco-conscious world, paper tube packaging is emerging as a game-changer in the sustainable packaging industry.
In today’s eco-conscious world, businesses are increasingly turning to sustainable packaging solutions.
Paper tube packaging has emerged as a game-changer in the world of sustainable packaging solutions.
In today’s packaging landscape, product safety is paramount.
© All Rights Reserved 2024