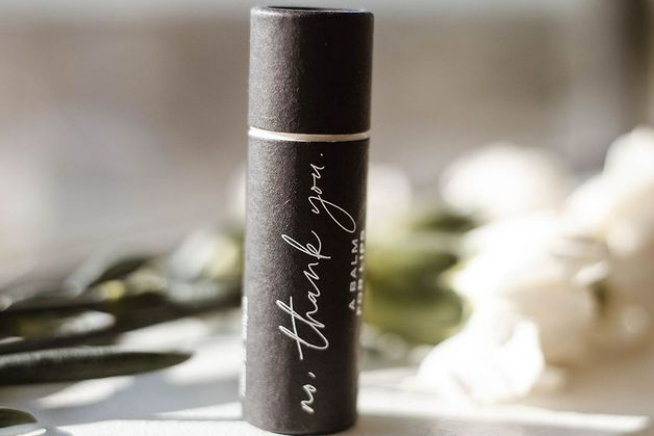
Unlocking Cost Savings: The Hidden Value of Paper Tube Packaging
Paper tube packaging is revolutionizing the way businesses approach their packaging needs.
Whether you’re in the packaging industry or simply interested in sustainable materials, understanding the best materials for kraft paper tubes is crucial. In this comprehensive guide, we’ll explore the ins andouts of paper tube manufacturing, focusing on the materials that make these versatile packaging solutions possible. From environmental considerations to practical applications, we’ll cover everything you need to know about creating high-quality kraft paper tubes. Let’s dive in!
Kraft paper has long been a favorite in the packaging industry, especially for tube manufacturing. But what makes it so special?Strength and durability are key factors that set kraft paper apart. The kraft process, which involves treating wood chips with chemicals to separate the cellulose fibers, results in a paper that’s remarkably strong for its weight. This strength is essential for paper tubes that need to withstand the rigors of shipping and handling.Another advantage of kraft paper is its versatility. It can be easily customized to meet various needs, whether it’s for shipping documents, storing posters, or packaging food products. The natural brown color of kraft paper also gives it a rustic, eco-friendly appeal that many consumers appreciate.
The manufacturing process for paper tubes plays a crucial role in determining the best material. Let’s break it down:
Each step of the process requires specific properties from the kraft paper, making material selection a critical decision for manufacturers.
Not all kraft paper is created equal. Here are some common types used in tube manufacturing:
The choice between these types depends on the specific requirements of the end product and the manufacturer’s priorities regarding cost, sustainability, and performance.
Paper weight, measured in grams per square meter (gsm), is a crucial factor in determining the strength of a paper tube. Generally, heavier paper weights result in stronger tubes, but there’s a balance to strike:
Manufacturers must consider the intended use of the tube when selecting the appropriate paper weight. A heavier paper will provide more strength but may also increase costs and the overall weight of the finished product.
The fiber composition of kraft paper significantly impacts its quality and performance in tube manufacturing. Here’s what you need to know:
In today’s eco-conscious world, environmental considerations play a significant role in material selection for paper tube manufacturing. Here are some key points to consider:
Balancing these environmental factors with performance requirements is crucial for manufacturers aiming to create sustainable packaging solutions.
Choosing the ideal material for kraft paper tubes isn’t without its challenges. Here are some common hurdles manufacturers face:
Overcoming these challenges requires a deep understanding of both the material properties and the specific needs of the end-user.
Quality control is paramount in kraft paper tube manufacturing. Here are some methods used to test and ensure material quality:
Regular testing and quality control measures help manufacturers maintain high standards and meet customer expectations consistently.
The world of packaging is constantly evolving, and kraft paper tube materials are no exception. Here are some trends to watch:
These innovations promise to expand the capabilities of kraft paper tubes, making them even more versatile and sustainable packaging solutions.
Selecting the best material for kraft paper tube manufacturing is a complex decision that requires careful consideration of various factors. From strength and durability to environmental impact and cost-effectiveness, each aspect plays a crucial role in determining the ideal material for your specific needs.Here are the key takeaways to remember:
By keeping these points in mind, you’ll be well-equipped to make informed decisions about the best materials for your kraft paper tube manufacturing needs. Remember, the right choice can lead to superior products, satisfied customers, and a more sustainable packaging industry overall.
Paper tube packaging is revolutionizing the way businesses approach their packaging needs.
In today’s eco-conscious world, businesses are increasingly turning to sustainable packaging solutions.
Food supplement paper tube packaging is transforming the way products are presented in retail environments.
Paper tube packaging is emerging as a game-changer in the pursuit of a circular economy.
In today’s world of sustainable packaging solutions, cardboard tubes have emerged as a versatile and eco-friendly option.
In today’s eco-conscious world, paper tube packaging is making waves in the consumer goods industry.
In today’s eco-conscious world, businesses are increasingly turning to sustainable packaging solutions.
Paper tube packaging has emerged as a game-changer in the world of sustainable packaging solutions.
In today’s packaging landscape, product safety is paramount.
© All Rights Reserved 2024